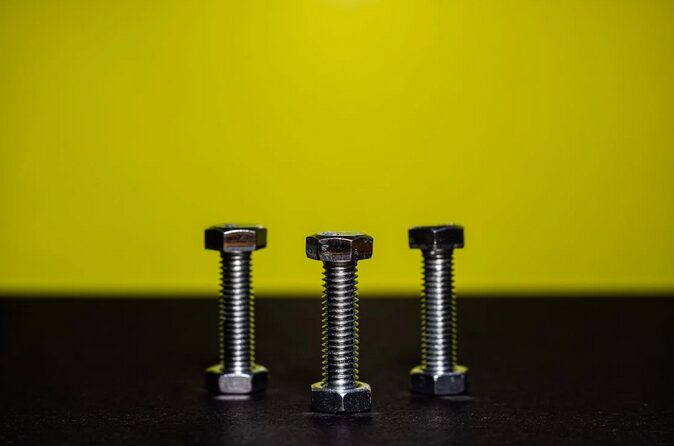
In manufacturing, precision is not just a goal—it’s a necessity. Every component must meet exact specifications to ensure the quality and functionality of the final product. One critical aspect of this precision is the use of thread gages. These tools used to measure the pitch and diameter of threads on screws, bolts, and other fasteners, play a vital role in ensuring that parts fit together perfectly. This article explores why precision in thread gauges is crucial in manufacturing and how it impacts production.
Ensuring Accurate Fit and Functionality
Thread gauges are essential for verifying that threaded components, such as screws and bolts, meet precise standards. Incorrect thread size can lead to parts not fitting together properly, resulting in assembly issues, product failures, or safety hazards. Manufacturers can use thread gauges to ensure each component meets the required specifications. This is critical for products that rely on secure, tight fits, such as machinery, automotive parts, and aerospace components.
Maintaining Consistency in Mass Production
Consistency is key in mass production. Manufacturers produce thousands of identical parts if not millions, and even a minor deviation in thread size can lead to significant problems. Thread gauges help maintain this consistency by providing a reliable method for checking that every part produced matches the exact specifications. This consistency is crucial in industries like automotive and aerospace, where even a small variation can compromise the safety and performance of the product.
Reducing Waste and Rework
Thread gauges’ precision also significantly reduces waste and rework in manufacturing. When components are not accurately measured, they may need to be scrapped or reworked, leading to increased material costs and production delays. By ensuring that threads are correct the first time, thread gauges help minimize these issues, resulting in more efficient production processes and lower overall costs.
Supporting Quality Control
Quality control is a critical aspect of manufacturing, and thread gauges are integral to this process. By using thread gauges during the inspection phase, manufacturers can detect deviations from the required specifications early on, preventing defective parts from reaching the final product. This proactive approach to quality control helps maintain high standards and ensures that only products that meet the strictest criteria are delivered to customers.
Ensuring Compliance with Industry Standards
In many industries, strict standards govern threaded components’ dimensions and tolerances. Thread gauges verify that these components comply with industry regulations, such as those set by the International Organization for Standardization (ISO) or the American National Standards Institute (ANSI). Compliance with these standards is essential for manufacturers to ensure their products are accepted in the global market and meet their customers’ safety and performance expectations.
Precision in thread gauges is vital in manufacturing and critical in ensuring the accuracy, consistency, and quality of threaded components. By using thread gauges, manufacturers can produce parts that fit together perfectly, maintain consistency in mass production, reduce waste and rework, support rigorous quality control processes, and comply with industry standards. In a world where precision matters more than ever, the role of thread gauges in manufacturing cannot be overstated. They are indispensable tools that help manufacturers achieve the high levels of accuracy required to deliver reliable, high-quality products.